New threaded bottom bracket molded directly into the carbon frame
The return of the threaded bottom bracket is already a fact and bike manufacturers are looking to evolve their manufacturing methods to get the maximum performance from this system thanks to technologies that did not even exist in the previous era where this type of bottom bracket was the standard. A clear example is the Canadian firm Bridge Bike Works, which has managed to mold the threads directly into the carbon.
The evolution of a classic
Until a decade or so ago, practically all bikes used a threaded bottom bracket system, either with English or BSA thread, or the more traditional Italian thread, limited only to models from that country of the most famous road bike brands.
Only Cannondale, with its peculiar BB30, which fitted the bearings directly into the bottom bracket shell and then clamped them with a small circlip, broke with what was considered the standard for this part of the bike.
RECOMENDADO
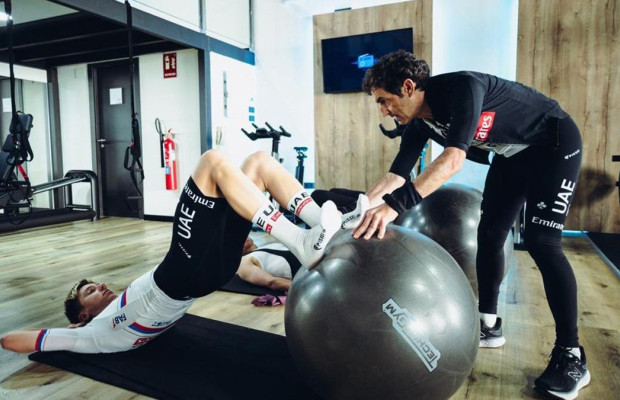
Injuries kept to a minimum, no equipment needed, and done in no time
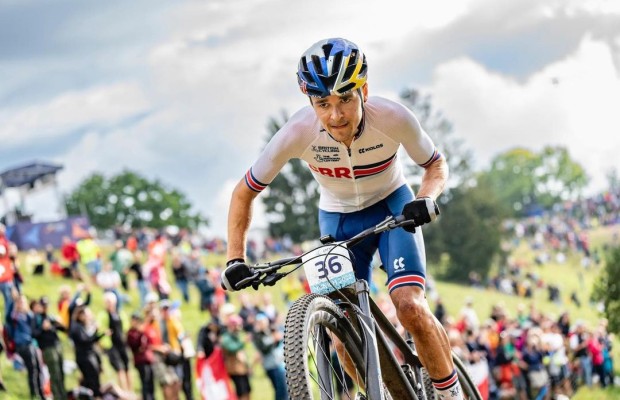
How much do top mountain bikers earn?
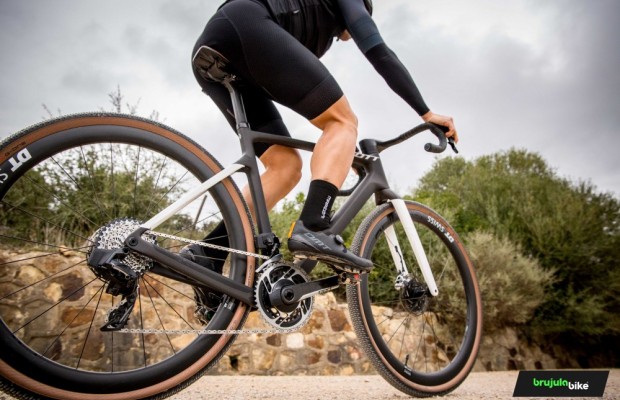
The best gravel groupsets of the moment
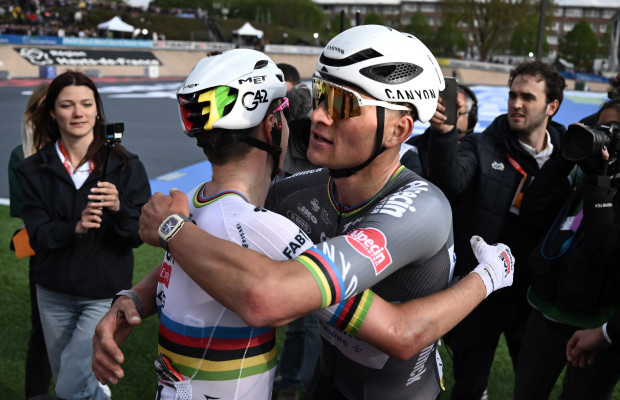
Complete list of the highest paid cyclists of 2025
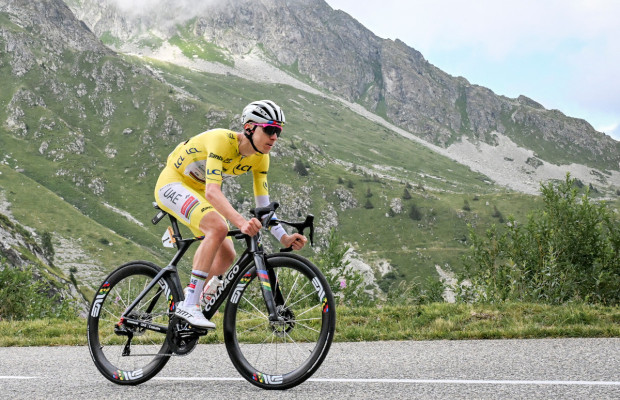
Pogacar joins the ranks of the cyclists with the most Grand Tours in history
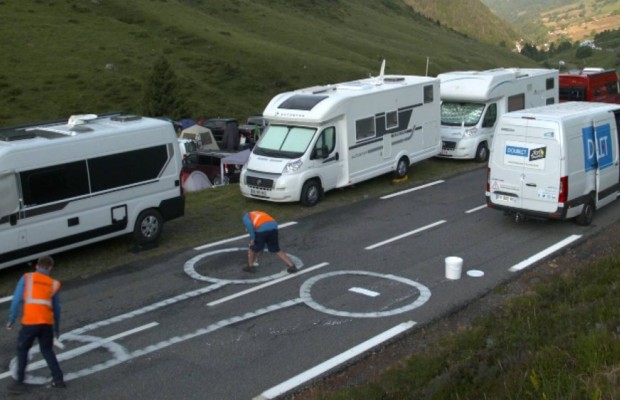
This is how they erase the penises that are drawn on the roads of the Tour de France
However, the search for greater lightness and simplification in the manufacture of carbon frames led to the evolution towards press-fit bottom brackets that were press-fitted into the frame structure itself. An apparently simple and reliable system but which, over time, proved to be very dependent on manufacturing tolerances, becoming a real headache for some manufacturers as a source of noise and play.
Finally, for some years now, bicycle manufacturers have been giving in and returning to threaded bottom bracket systems. In some cases with the T47 designed to accommodate cranks with 30 mm axle but, in most cases, pressured by the all-powerful Shimano when mounting their complete groupsets, opting for the traditional BSA.
Threaded bottom brackets are much easier to maintain as they are easy to remove and install and do not compromise the frame structure. However, their weak point is still the one that led to their removal: they require an aluminum bushing glued to the frame to house the thread, which increases the weight and can be a source of failure in an area that receives as many stresses as the bottom bracket shell.
Something that could change with technologies such as the one shown by the Canadian brand Bridge Bike Works that have been able to mold the threads of the bottom bracket threads directly on the carbon and that could lead the way in the not too distant future.
The brand obviously states that this solution is reliable and even more resistant than metal bottom brackets, avoiding the possibility of corrosion caused by humidity and dirt that can lead to the threaded cups being literally welded to the bushings, saving about 100 g compared to the usual solution.
Bridge also ensures that its molded bottom bracket system, in this case a T47, maintains perfect cup alignment, a critical detail to avoid bearing noise and creaking.
Undoubtedly an interesting contribution towards the improvement of a system that has hardly changed since the days of steel bikes and yet has returned as the most reliable option to provide the necessary pivot point from which the force of our legs is transferred to the bike. Who knows if more brands will also dare to integrate their threads into carbon.