Are aluminum wheels more resistant than carbon wheels?
Despite the evolution of carbon wheels, they still generate certain reservations among cyclists who doubt their resistance, especially among those cyclists who pedal off the asphalt in modalities such as gravel or mountain biking. However, the level of manufacturing achieved today makes carbon-made wheels tremendously efficient for many thousands of kilometers.
Are carbon wheels reliable?
The presence of carbon wheels seems to have normalized in recent years, especially in high-end models. However, many cyclists are still wary of their use, which leads many to reserve them for special days or even to continue trusting in aluminum models.
These reservations may come from the early days of this type of wheel when they were more delicate models. The arrival of carbon wheels for tyres also did a lot of damage to the confidence in carbon wheels, which had numerous breakage problems caused by the overheating of the rim caused by the brake pads, a problem overcome since disc brakes are the norm.
RECOMENDADO

Change wheels if you want to transform your bike's behavior
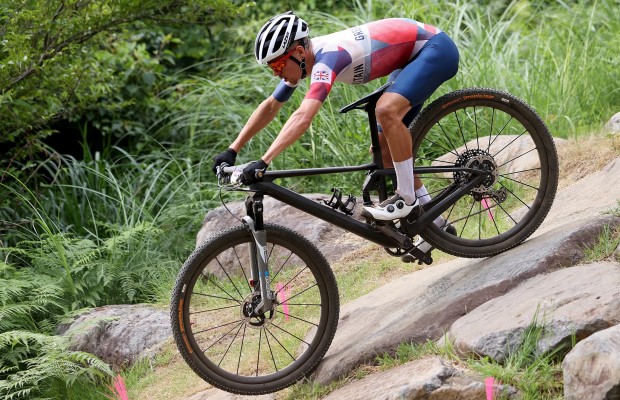
What bike size do you need? Here's how to find out
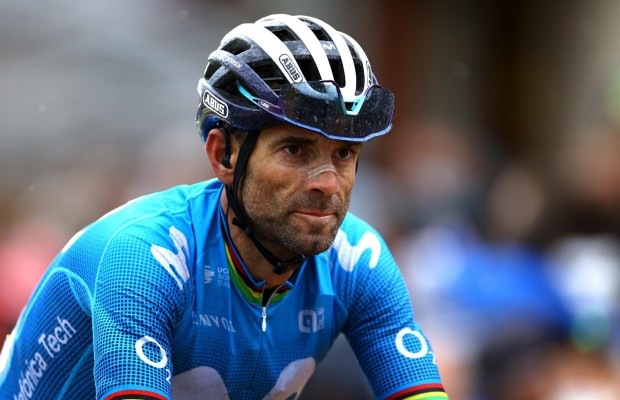
How does age affect performance and recovery?
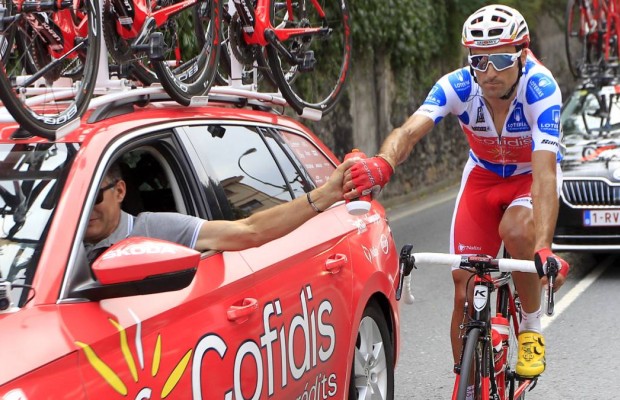
How long cyclists can be pushed when handed a sticky bottle?
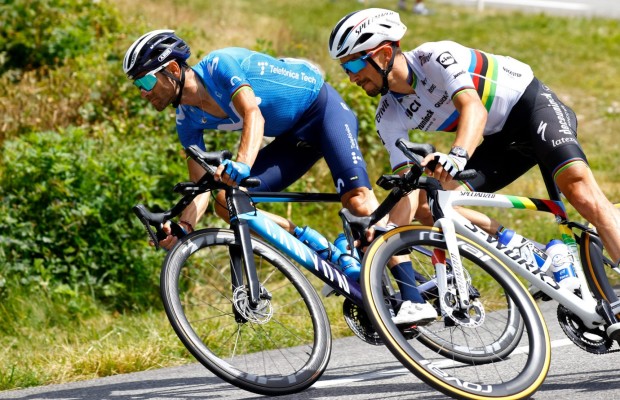
10 tips for safer and faster downhills on road bikes
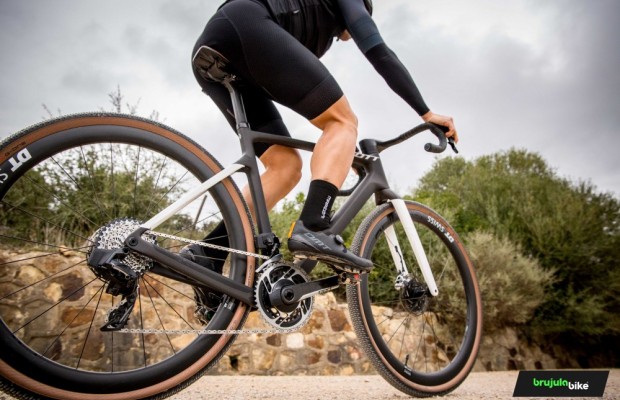
The best gravel groupsets of the moment
On the other hand, aluminum rims have been used for decades and it is a material that has proven to be very reliable when it comes to withstanding hard treatment, being able to withstand impacts without breaking. Perhaps this is the main difference between aluminum and carbon rims. An aluminum rim can receive impacts and deform, however, the carbon one, if it receives a force greater than it can resist, it breaks.
Precisely the evolution in carbon wheels has been to create increasingly worked laminates to be able to resist increasingly high forces, even far exceeding the minimums set by the UCI to approve a wheel model to be used in competition.
The resistance of a carbon structure such as a frame or a wheel depends largely on the placement of the fibers depending on the stresses it has to withstand. If the forces are exerted in the direction of the carbon weave, the resistance of this material is enormous, but it drops a lot if these forces are applied transversely.
As for aluminum, while it is more difficult for a total breakage to occur in a rim made with this type of material, it does have a weak point: the fatigue of the material. And it is that with use it weakens until one day it ends up yielding, either in the form of a crack or directly breaking, something that does not happen with carbon.
To improve reliability, carbon wheel manufacturers have been working for years to optimize laminates in addition to applying better qualities of fiber that are appearing and resins that provide new and better properties. The goal is to raise that breaking limit to a figure that is extremely difficult to reach in normal use, even in the event of a crash or impact, a limit that, obviously, is much higher than that achieved with any aluminum rim.
The evolution is such that today we have wheels designed to be used in off-road disciplines that are totally reliable and that, in case of failure, are designed so that there is redundancy of fibers that makes a total breakage never occur that could put us in danger, for example if it occurs in a high-speed descent.